O que são Sistemas SCADA?
Os Sistemas SCADA, acrônimo para Supervisory Control and Data Acquisition, representam uma solução avançada de automação industrial desenvolvida para monitorar e controlar processos industriais em tempo real. Essas tecnologias são amplamente adotadas em diversos setores, incluindo energia, água e saneamento, manufatura, transporte e muito mais. A funcionalidade dos sistemas SCADA consiste em coletar dados de sensores, dispositivos e equipamentos distribuídos por uma instalação. Esses dados são então processados e apresentados de forma que os operadores possam monitorar a operação e a performance do sistema com relativa facilidade.
A origem dos sistemas SCADA remonta à década de 1960, quando os primeiros sistemas para controle remoto começaram a ser implementados. Inicialmente, os sistemas eram limitados em termos de capacidade de processamento, mas a evolução tecnológica permitiu que essas ferramentas se tornassem mais sofisticadas ao longo dos anos. Nos anos 80, a introdução de interfaces gráficas de usuário e computadores pessoais revolucionou a forma como as informações eram apresentadas, tornando-as mais acessíveis e intuitivas. Esse avanço foi crucial para a disseminação do uso dos sistemas SCADA na indústria.
Hoje, os sistemas SCADA não apenas monitoram dados, mas também oferecem funcionalidades de automação, como o controle de processos e a gestão de alertas e alarmes em tempo real. À medida que a Indústria 4.0 avança, a integração de SCADA com tecnologias emergentes, como IoT (Internet das Coisas) e análise de dados, percorre novas fronteiras, tornando os processos industriais ainda mais eficientes e responsivos. Dessa forma, os sistemas SCADA continuam a desempenhar um papel vital, adaptando-se às novas demandas e contribuindo significativamente para a modernização da indústria global.
Como Funcionam os Sistemas SCADA?
Os Sistemas de Controle e Aquisição de Dados (SCADA) são fundamentais para a automação industrial, proporcionando uma análise em tempo real dos processos de produção. Eles são compostos por uma série de elementos interconectados, que trabalham juntos para monitorar e controlar operações industriais. Entre os principais componentes estão os sensores, controladores, e as interfaces de usuário. Os sensores coletam dados físicos, como temperatura, pressão ou fluxo, e enviam essas informações aos controladores, que processam os dados e executam ações corretivas, se necessário.
As interfaces de usuário desempenham um papel crucial, permitindo que os operadores visualizem dados processados e tomem decisões informadas com base em gráficos, relatórios e alertas. Esta visualização é muitas vezes facilitada por meio de painéis de controle intuitivos, que oferecem uma visão abrangente do status de produção e ajudam na identificação de possíveis falhas antes que se tornem críticas. Um exemplo prático da aplicação de sistemas SCADA pode ser encontrado na indústria de petróleo e gás, onde sensores monitoram a pressão em oleodutos e informam os controladores para evitar acidentes.
As conexões e protocolos de comunicação são outros elementos vitais que asseguram a eficácia dos sistemas SCADA. Protocolos como Modbus e DNP3 possibilitam a troca de informações entre dispositivos remotos e a unidade central, permitindo a aquisição de dados em tempo real. Essas conexões podem ser realizadas através de redes cabladas ou sem fio, dependendo das necessidades específicas de cada operação. A integração eficaz dessas tecnologias não só melhora a eficiência operacional, mas também garante a segurança e a confiabilidade dos processos industriais.
Monitoramento em Tempo Real
O monitoramento em tempo real é um dos benefícios mais significativos proporcionados pelos sistemas SCADA (Supervisory Control and Data Acquisition) na automação industrial. Esses sistemas oferecem uma visualização clara e instantânea de dados operacionais, permitindo que os gestores e operadores acompanhem o desempenho de processos críticos em tempo real. Isso se traduz em uma tomada de decisões mais ágil e informada, essencial em ambientes industriais onde o tempo e a precisão são fundamentais.
Com a capacidade de acompanhar indicadores-chave de desempenho, as indústrias podem identificar rapidamente quaisquer desvios nos processos operacionais. Por exemplo, em uma fábrica de produção, se o sistema SCADA detectar uma queda súbita na temperatura de um forno, a resposta imediata pode evitar a produção de produtos defeituosos ou até mesmo danos ao equipamento. Essa capacidade de resposta rápida, possível pelo monitoramento em tempo real, não só preserva a qualidade do produto, mas também minimiza custos e perdas associadas a falhas operacionais.
Além disso, o monitoramento em tempo real permite uma análise contínua do desempenho, o que pode levar a melhorias incrementais nos processos produtivos. Por meio da coleta e visualização de dados em tempo real, os engenheiros podem identificar tendências e padrões que antes passariam despercebidos, proporcionando informações valiosas para otimização dos processos. Por exemplo, em setores como a petroquímica, a monitoração constante dos níveis de pressão e temperatura em ambientes de alta pressão pode resultar em processos mais seguros e eficientes.
Esses exemplos demonstram que o monitoramento em tempo real, viabilizado pelos sistemas SCADA, não apenas melhora a eficiência operacional das indústrias, mas também proporciona um ambiente de trabalho mais seguro e controlado. Com a visualização imediata de dados e indicadores, as empresas são mais bem equipadas para enfrentar desafios operacionais e se adaptar rapidamente às mudanças exigidas pelo mercado.
Controle de Processos Industriais
Os sistemas SCADA (Supervisory Control and Data Acquisition) desempenham um papel crucial no controle e automação de processos industriais. Esses sistemas permitem o monitoramento e controle em tempo real de operações, possibilitando uma gestão eficiente de recursos. Um exemplo notável é o uso de sistemas SCADA na indústria de manufatura, onde a automação de linhas de produção não apenas melhora a precisão dos processos, mas também aumenta significativamente a eficiência operacional.
Com a adoção de sistemas SCADA, as empresas podem reduzir consideravelmente os custos operacionais. Ao automatizar o controle de máquinas e equipamentos, os erros humanos são minimizados, resultando em menos falhas e retrabalho. Isso é especialmente relevante em setores que exigem altos padrões de qualidade e consistência, como a produção de alimentos e bebidas, farmacêutica e automotiva. A implementação de técnicas de controle automatizado, como o controle PID (Proporcional, Integral, Derivativo), fornece uma resposta precisa às variações nas condições de operação, garantindo que os processos permaneçam dentro de parâmetros operacionais desejados.
Além disso, os sistemas SCADA oferecem funcionalidades de alerta e notificação em casos de anomalias, permitindo que as equipes de manutenção intervenham rapidamente antes que se tornem problemas maiores. A combinação de monitoramento em tempo real e controle automático resulta em processos mais eficientes e de maior qualidade. Por exemplo, estudos mostraram que a utilização de sistemas SCADA em uma planta de processamento reduziu o desperdício de matérias-primas em até 20%, exemplificando como o controle automatizado pode levar a significativas economias financeiras.
Portanto, é evidente que os sistemas SCADA transformam a maneira como as indústrias controlam seus processos, contribuindo para uma produção mais eficiente, segura e rentável.
Aumento da Eficiência e Produtividade
A implementação de sistemas SCADA (Supervisory Control and Data Acquisition) na automação industrial tem demonstrado um impacto significativo na eficiência e produtividade das operações. Um dos principais benefícios desses sistemas é sua capacidade de monitorar e controlar processos em tempo real, permitindo que as empresas ajustem imediatamente as operações conforme necessário. Isso resulta em processos mais rápidos e contínuos, minimizando o tempo de inatividade e aumentando a produção geral.
As métricas de desempenho associadas à adoção de SCADA revelam melhorias notáveis. Com a automação, é possível coletar dados detalhados sobre cada etapa do processo produtivo. Esses dados não apenas ajudam a identificar gargalos e ineficiências, mas também são utilizados para prever falhas e agendar manutenções preventivas. Isso garante que os equipamentos estejam sempre operacionais, reduzindo interrupções inesperadas e melhorando a disponibilidade operacional.
Um exemplo claro dessa melhoria pode ser observado em uma grande empresa do setor petroquímico, que após a implementação de um sistema SCADA, conseguiu elevar sua taxa de produção em 20% em apenas seis meses. O acesso em tempo real às operações permitiu aos gestores tomar decisões mais informadas, além de otimizar o uso de recursos, como energia e materiais, que são cruciais no processo produtivo.
Além disso, os sistemas SCADA proporcionam uma integração mais eficiente entre diferentes áreas da produção. Isso se traduz em uma abordagem mais holística para a gestão industrial, onde cada parte do processo está interconectada e pode ser ajustada conforme as exigências do mercado. A resultante sincronização entre departamentos como produção, qualidade e logística é vital para o sucesso da automação industrial.
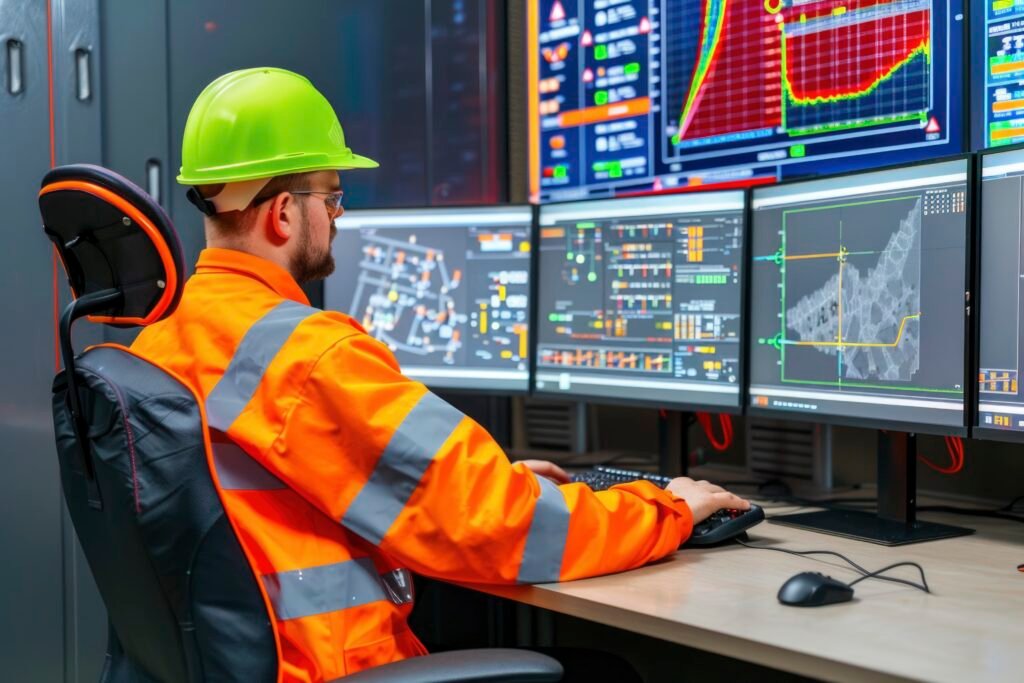
Manutenção Preditiva Através do SCADA
A manutenção preditiva é uma abordagem que visa antecipar falhas em sistemas industriais antes que elas ocorram, permitindo uma gestão mais eficiente dos recursos e a redução de custos operacionais. Os sistemas SCADA (Supervisory Control and Data Acquisition) desempenham um papel fundamental nesse contexto, utilizando dados em tempo real para monitorar o desempenho dos equipamentos e identificar sinais que possam indicar falhas iminentes.
Uma das principais vantagens dos sistemas SCADA na manutenção preditiva reside na sua capacidade de coletar e analisar grande volumes de dados de sensores e de outros dispositivos conectados. Essa análise permite o rastreamento contínuo das condições de operação, como temperatura, pressão e vibração. Quando esses parâmetros começam a desviar de suas faixas normais de operação, a plataforma SCADA gera alertas que podem ser utilizados para programar intervenções antes que ocorram falhas catastróficas. Ao implementar essa abordagem, as empresas minimizam o tempo de inatividade não planejado, resultando em um aumento significativo na eficiência operacional.
Além disso, a integração de algoritmos de aprendizado de máquina nos sistemas SCADA pode aprimorar ainda mais a manutenção preditiva. Esses algoritmos são capazes de identificar padrões invisíveis aos operadores humanos, potencializando a detecção de falhas em estágios iniciais. A combinação da análise preditiva com planejamento estratégico proporciona uma abordagem proativa em vez de reativa, permitindo que as empresas priorizem os recursos de manutenção de maneira eficaz.
Consequentemente, a utilização dos sistemas SCADA para gerenciar a manutenção preditiva representa uma transformação crucial para as estratégias de manutenção nas indústrias. Através da análise contínua de dados e do uso inteligente da tecnologia, as empresas conseguem não apenas reduzir custos, mas também aumentar a segurança operacional e a confiabilidade dos seus equipamentos.
Segurança e Confiabilidade
Nos ambientes industriais contemporâneos, a segurança e confiabilidade dos Sistemas de Controle e Aquisição de Dados (SCADA) são de suma importância para assegurar a integridade das operações. A proteção dos dados e processos industriais é um aspecto crítico, dado que qualquer vulnerabilidade pode resultar em sérias consequências, incluindo perda de produção, danos a equipamentos e riscos à segurança dos funcionários. Medidas de segurança adequadas são, portanto, essenciais.
Uma das principais estratégias de segurança implementadas em sistemas SCADA é a segmentação de redes. Isso implica dividir a rede industrial em diferentes segmentos, limitando o acesso e minimizando os pontos de falha potencial. Além disso, a implementação de controles de acesso rigorosos, como autenticação multifatorial, ajuda a garantir que apenas indivíduos autorizados possam interagir com o sistema. Monitoramento contínuo e auditorias regulares são práticas recomendadas que permitem a detecção precoce de atividades suspeitas.
Outra preocupação significativa é com a proteção contra ameaças cibernéticas. O aumento dos ataques digitais, como malware e ransomware, exige que as empresas adotem um protocolo de defesa em profundidade. Isso inclui a utilização de firewalls, software de detecção de intrusões e a realização de atualizações de software e patches regularmente. Os sistemas SCADA também devem ser configurados de modo a limitar a exposição a redes externas, combatendo assim tentativas de acesso não autorizado.
Além das medidas técnicas, a conformidade com regulamentações e normas de segurança é fundamental. Normas como a ISO/IEC 27001 e diretrizes de instituições como a NIST (National Institute of Standards and Technology) oferecem um framework para a implementação de práticas de segurança eficazes. Ao seguir essas melhores práticas e regulamentações, as organizações podem aprimorar significativamente a segurança e confiabilidade de seus sistemas SCADA, protegendo não apenas os dados, mas também a continuidade das operações industriais.
Integração com Outras Tecnologias
A integração de sistemas SCADA (Supervisory Control and Data Acquisition) com tecnologias emergentes, como Internet das Coisas (IoT), Big Data e Inteligência Artificial, tem se mostrado uma tendência crescente na automação industrial. Esta convergência tecnológica permite a criação de redes mais eficientes, onde os dispositivos podem coletar e transmitir dados em tempo real, resultando em uma infraestrutura industrial mais inteligente.
Um dos principais benefícios dessa integração é a capacidade de análise aprimorada. Ao combinar dados coletados de dispositivos IoT com sistemas SCADA, é possível gerar análises de desempenho mais precisas e identificar padrões que tradicionalmente poderiam passar despercebidos. As soluções baseadas em Big Data possibilitam o armazenamento e processamento de grandes volumes de informações, o que é fundamental para melhorar a tomada de decisões nas operações industriais. A utilização de algoritmos de aprendizado de máquina pode ainda otimizar essas análises, permitindo previsões mais acertadas sobre falhas e manutenção preventiva.
Outra vantagem significativa é a capacidade de monitoramento remoto. Sistemas SCADA integrados com IoT proporcionam a supervisão de equipamentos e processos a partir de diferentes locais, garantindo que os operadores tenham acesso a informações críticas sempre que necessário. Essa flexibilidade não apenas melhora a eficiência operacional, mas também diminui os custos associados à necessidade de presença física constante nas instalações.
Além disso, a interoperabilidade entre SCADA e outras tecnologias prepara as indústrias para os desafios do futuro, permitindo uma adaptação mais fácil a novas ferramentas e práticas. As empresas que adotam essa abordagem não apenas se posicionam como líderes em inovação, mas também asseguram uma maior sustentabilidade e competitividade em um mercado em constante evolução.
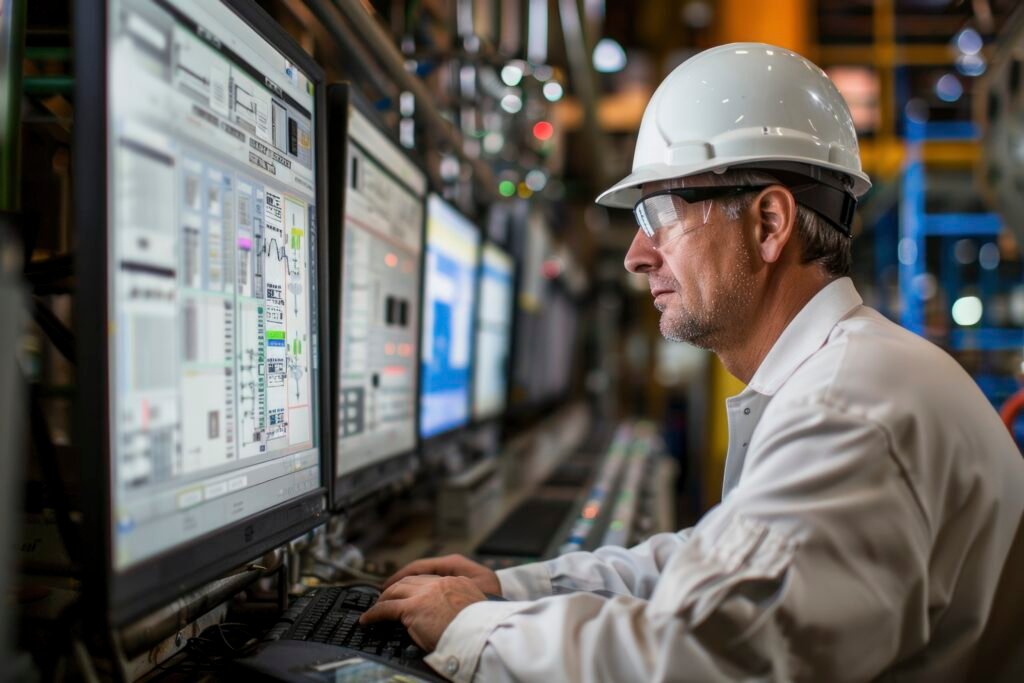
Os sistemas SCADA têm se mostrado fundamentais na automação industrial, proporcionando uma gestão eficiente e eficaz dos processos produtivos. Ao longo deste post, discutimos diversos benefícios trazidos por essas plataformas, como a supervisão em tempo real, a coleta de dados históricos e a capacidade de resposta rápida a incidentes. Com a integração de tecnologias avançadas, como a Internet das Coisas (IoT) e a análise de big data, os sistemas SCADA podem se tornar ainda mais robustos, oferecendo insights valiosos para garantir a continuidade das operações e aumentar a eficiência.
No futuro, podemos esperar um desenvolvimento contínuo dos sistemas SCADA, com um foco crescente em melhorias na cibersegurança e na automação autônoma. À medida que as indústrias se tornam cada vez mais interconectadas, a necessidade de sistemas SCADA que possam operar de forma coesa com outros componentes e plataformas tecnológicas será crucial. A inovação em inteligência artificial e machine learning promete transformar a maneira como esses sistemas coletam e analisam dados, por exemplo, antecipando falhas antes que elas ocorram e otimizando a manutenção preditiva.
Além disso, a adoção de plataformas baseadas em nuvem é uma tendência emergente, já que permite um acesso fácil a dados em qualquer lugar e a qualquer momento. Isso não só melhora a colaboração entre equipes, mas também facilita a implementação de soluções escaláveis que podem acompanhar o crescimento das operações industriais. A importância contínua dos sistemas SCADA no setor industrial é indiscutível e sua evolução promete trazer melhorias significativas nas práticas de automação, garantindo um futuro mais inteligente e eficiente para a indústria.
Para as empresas que buscam se destacar em um mercado competitivo, a automação não é apenas uma opção, é uma necessidade. Invista em soluções inteligentes com a Engenharidade e descubra como a automação pode impulsionar o crescimento e a lucratividade do seu negócio.